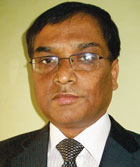
SK Singh, Principal Scientist, Dharmendra Singh, and Chanchal Sonkar, Trainee Scientist, CSIR- Central Building Research Institute, Roorkee, India.
Introduction
The modern construction industry uses a variety of chemical admixtures in concrete, to reach desirable qualities along with a view to promote sustainability in it. ASTM C 125 defines an admixture as a material other than water, aggregate, cement, and fiber reinforcement, used as an ingredient of concrete mortar and added to the batch immediately before or during mixing. Chemical admixtures are the smallest component of a concrete mix but impart significant beneficial effects on the concrete properties in terms of performance, durability, environment optimization leading to sustainability etc. The incorporation of admixtures in concrete mix has been recognized as an important and integral means to modify and improve performance of concrete at both fresh as well as hardened states. Admixtures should never be regarded as a substitute for a good mix design, good workmanship or use of good materials. There are several chemical admixtures that include water reducers, accelerators, anti-freezing admixtures, air-entraining admixtures, alkali-aggregate inhibitors, shrinkage compensating admixture, and corrosion inhibitors etc. Figure 1 shows some of the chemical admixtures meant for use in cement concrete.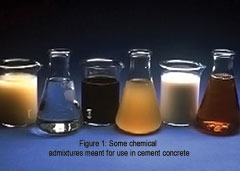
- To increase workability without changing water content
- To reduce water content without changing workability
- To effect a combination of above
- To adjust setting time
- To reduce segregation and/or bleeding
- To accelerate the rate of early strength gain
- To improve pumpability
- To increase strength
- To improve potential durability and reduce permeability
- To reduce the total cost of the materials used in the concrete
- To compensate for certain poor aggregate grading/properties
- To depress the freezing point of water in concrete at very low temperatures (up to minus 30°C)
- To maintain adequate freezing and thawing resistance of concrete
- To inhibit alkali-aggregate reactions (AAR)
{akeebasubs !*}
Click here to read complete article.{/akeebasubs} {akeebasubs *}
Water Reducing Admixtures

Normal water-reducing admixtures are used to reduce water requirements up to 15%. A higher dosage of a normal water-reducing admixture leads to cause excessive set retardation and air entrainment. These admixtures are categorized as given below according to their active ingredients:
- Salts and modifications of hydroxylized carboxylic acids (HC type)
- Salts and modifications of lignosulfonic acids (lignins type)
- polymeric materials (PS type)
Superplasticizers
Superplasticizers are key components of a durable and sustainable concrete. The use of superplasticizers in concrete is not new. These have been in use since the early 1970s. Their use makes it possible to design concrete at lower water-to-binder ratio than the normal water reducing agents. It is widely accepted that concretes having a low water-to-binder ratio are more environment friendly than the usual 20 – 30 MPa concretes. Their use results in saving of materials and reduction in greenhouse gas emissions associated with manufacturing and use of concrete. Superplasticizers can be used to reduce the water requirement up to 30% or even more for a given workability without adversely affecting the setting and air entraining of concrete mixes as in the case of a normal water reducing admixture. The superplasticizers are composed of synthetic water-soluble polymers. These include sulfonated melamine formaldehyde (SMF) or sulfonated naphthalene formaldehyde (SNF) condensate. Due to the lower cost of lignosulfates, attempts were made to make lignosulfate-based superplasticizers. Performances of lignosulfate-modified superplasticizers have been reported to be similar to unmodified melamine or naphthalene-based superplasticizers3. Recently, a new family of superplasticizer, known as polycarboxylates or polyacrilates, has been developed. The dispersion of cement particles by this family of superplasticizers are due to steric repulsion rather from electrostatic repulsion which occurs in polysulfonated superplasticizers4. The ability of superplasticizers to increase the slump of concrete depends on such factors as the type, dosage and time of addition of superplasticizers, W/C, and cement types and its dose / amount.One common problem associated with the use of superplasticizers in concrete is slump loss. Generally, slump loss occurs after 30 - 60 minutes of addition of superplasticizers in concrete mixes. In order to offset this effect, several methods have been recommended. One of the methods suggested to overcome this problem advocates the addition of the superplasticizer just before placement of the concrete. Other methods include redosing the superplasticizer at different time intervals with or without inclusion of retarder. Depending upon the method of application, variability in slump or strength development can occur. Additionally, total amount of superplasticizer will also vary depending upon the method of application. For the control of quick slump loss, a new superplasticizers family based on Carboxylated Acrylic Ester (CAE) copolymer has been developed5. This contains carboxylic (COO-) groups in place of sulfonic (SO3-) groups. This new superplasticizer showed excellent performance in controlling slump loss6. Several other superplasticizers, as described by Ramachandran3 and Collepardi6 which can control the workability of concrete to a marked extent, are also available. However, performance of new superplasticizers in concrete under a wide range of conditions is yet to be established.
Compatability and Robustness of Cement/Superplasticizer Combinations
Different behaviors of cement/superplasticizer combinations are commonly encountered in practice as not all cement/superplasticizer combinations are equally efficient in dispersing cement particles. Some combinations are compatible i.e. they maintain the initial slump for more than 15 minutes. Further, it has been observed that some cement/superplasticizer combinations are robust that is, the effect of small variation in the cement, water, and superplasticizer dosage have little influence on the rheological behavior of the concrete. On the other hand, in other combinations of cement/superplasticizer a small variation in the cement, water or superplasticizer dosage makes concrete non-robust. Therefore, from a practical point of view it is much safer to work with a cement/superplasticizer combination which is more robust. These different behaviours of cement/superplasticizer combinations are due to the fact that not only the main phases of the cement particle interact with superplasticizer molecules but the minor components such as calcium and alkali sulphates also interact. The phase composition of cement as well as minor components varies from one clinker to another even at same plant. A phase difference on the surface of the cement particles has a very important role on the cement/superplasticizer combinations as the superplasticizer molecules initially act only on the surface of cement particle.The efficiency of a superplasticizer also depends on the solid content of the admixtures. The solid content of superplasticizers varies from 15% to 40%. The dosages of a superplasticiser are expressed in different ways. It is often expressed in liters of superplasticizer solution per cubic meter of concrete. But such expression may result in serious mistake if the solids content and specific gravity of the admixtures changes. For example, melamine superplasticizers can be found as a liquid solution having 22%, 33%, 40% of solid contents, therefore, their respective dosages will be different according to the solid contents. Hence, it is always better to express dosages of superplasticizers with solid content and as a percentage of the mass of cement used in the concrete mix. Therefore, evaluation of cement/superplasticizer compatibility and robustness and proper expression of dosage of superplasticizer mentioning the solids content are very important.
Evaluation of Cement/Superplasticizer Compatibility and Robustness
Cement/superplasticizer compatibility and robustness depend not only on certain specific properties of the cement and the superplasticizer, but also on their conditions of use. Their interaction is studied using two simple comparative tests:- The mini-slump test
- The marsh-cone test
Commercial superplasticizers are made either from pure base or from a mixture of a pure base and other admixtures. Other admixtures are mixed to improve the efficiency of the base with certain types of cements. In some cases, chemical admixture companies add a small amount of accelerator, retarder etc. Therefore, the basic knowledge is very important in order to check a particular combination of cement/superplasticizer combination. Further, verification tests should be carried out on the superplasticizers solution to ensure that the same material that was approved is being used. The commonly used identifying tests include chloride, solids content and pH of the superplasticizer solution.
Uses of Superplasticizers
Superplasticizers are used for the same purpose as shown in Figure 2 i.e. to increase concrete slump, to decrease W/B for a given slump and to combination of the both. The first use i.e. to increase concrete slump is very suitable in the precast industry or for making self-compacting concrete (SCC). The third use is exploited in making durable concrete (high strength and high impermeable concrete) at lower water–to- binder ratio.Accelerators
These chemical admixtures are added to concrete for the following purposes:- To increase the rate of early strength development
- To shorten the time of setting or both
The effects of these admixtures on concrete properties need to be established prior to their large-scale use in concrete. Additionally, compatibility of these admixtures with normal admixtures needs to be established under varying curing conditions.
Set Control or Set-Retarding Admixtures
These are admixtures used to delay hydration of cement without affecting the long-term mechanical properties of concrete. Retarders are used to offset the effect of high environmental temperatures or to avoid complications when unavoidable delays between mixing and placing of concrete occur. Many water reducing agents have a retarding tendency. Some of the ingredients of water reducers such as lignosulfate acids and hydroxycarboxylic acids are a basis for set-retarding. Other materials used for the purpose are sugars and their derivatives. These admixtures form a film around the cement particles thereby preventing or slowing the hydration reaction of cement particles. The thickness of the film determines how much the rate of hydration is retarded. The degree of retardation is also influenced by the W/C, cement content, C3A and alkali content, type and dosages of admixture and the stage at which the retarder is added to a concrete mix. Similar to other admixtures verification tests should be performed on retarders also.Summary and Conclusions
Various chemical admixtures such as water reducing agents, superplasticizers, accelerators, retarders, etc. are commonly used to either allow placement of concrete under different and/or difficult conditions and/or to improve performance of concrete so as to contribute to the sustainability of concrete industry. These admixtures are used to reduce consumption of energy and materials in the construction of infrastructures. The most widely used concrete admixture in our country is water reducing agents including superplasticizers. Water reducing agents are the key components of modern concretes. Their use results in higher fluidity, higher strength, higher durability, saving of materials etc. leading to sustainable development in the field of construction industry. Their appropriate use improves concrete sustainability. A proper understanding of the efficiency of the chemical admixtures, their compatibility with cement, their total solid content, etc. are very important to harness appropriate benefits of using these materials in concrete. Blind follow of the salesman advices should be avoided. Verification tests should be conducted to ensure the quality of admixtures being used in the construction work.- Admixtures should never be regarded as a substitute for a good mix design, good workmanship or use of good materials.
- The use of admixtures requires a proper understanding of their actions and not a blind follow of the advice of a salesman.
- It is much safer to work with a cement /superplasticizer combination which is more robust.
- It is always better to express dosages of superplasticizers or chemical admixtures with solids content and as a percentage of the mass of cement used in the concrete mix.
- Verification tests should be carried out on the superplasticizers solution to ensure that the same material that was approved is being used.
- The effects of accelerating admixtures on concrete properties need to be established prior to their large-scale use in concrete. Additionally, compatibility of these admixtures with normal admixtures needs to be established under varying curing conditions.
- The effects of retarding admixtures on fresh concrete properties need to be established prior to their large-scale use in concrete.
References
- Dodson, V. (1990). "Concrete admixtures." Van Nostrand Reinhold, New York.
- Rixom, M.R. and Mailvaganam, N.P. (1999). "Chemical admixtures for concrete." E & FN Spon, London.
- Ramachandran, V.S. (1994). "Recent progress in the development of chemical admixtures." in Advances in Concrete Technology, V.M. Malhotra, Ed., Second Edition, CANMET, Ottawa, Ontario, Canada, 785-838.
- AÏtcin, P-C and Mindess, S. (2011). "Sustainability of concrete." Spon Press, New York.
- Collepardi, M., Coppola, L., Cerulli, T., Ferrai, G., Pistolesi, C., Zaffaroni, P., and Quek, F. (1993). "Zero slump loss superplasticized concrete." Proceedings of the Congress, "Our World in Concrete and Structures," Singapore, 73-80, as reported by Collepardi (1994).
- Colleardi, M. (1994). "Advances in chemical admixtures for concrete." in Advances in Cement and Concrete, Proceedings of Engineering Foundation Conference, M.W. Grutzek and S. L. Sarkar, Eds., ASCE, New York, 257-291.
- Rixom, M.R. and Mailvaganam, N.P. (1986). "Chemical admixtures for concrete." Cambridge, England: The University Press.
Acknowledgements
The author is grateful to the Director, CSIR-Central Road Research Institute for his permission to publish the paper. Adarsh and Garima deserve special thanks for their help in the preparation of the manuscript.{/akeebasubs}