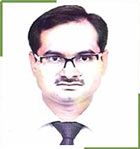
Concrete is one of the most commonly used building and construction materials. However, due to its composition, is often susceptible to damage and deterioration from water and chemical penetration. Concrete can be considered as a micro porous and permeable material. Porosity refers to the amount of voids left in concrete, is expressed as a percentage of the total volume of a material. Permeability expresses that how well the voids are connected.
Therefore, these qualities results pathways to form that allow the ingress and movement of water into, and through, along with the cracking that occurs due to shrinkage. Thus, these voids, pores and capillaries become the major sources for water leakages from the concrete structures.
Therefore, these qualities results pathways to form that allow the ingress and movement of water into, and through, along with the cracking that occurs due to shrinkage. Thus, these voids, pores and capillaries become the major sources for water leakages from the concrete structures.
Crystalline Waterproofing Technology
Although crystalline waterproofing technology has been around for more than 3 decades, it is still considered "state-of-the-art" and has only recently been embraced by the construction industry as a superior replacement for conventional membranes. Crystalline waterproofing systems rely on a technology that turns porous concrete in to an impermeable barrier. The result is a structure with reduced cracking, self-sealing and waterproofing abilities which provides a powerful defense against water damage and corrosion of reinforcing steel.
Unlike sheet membranes, which rely on an additional hurdle to shield the concrete from moisture, crystalline waterproofing system actually transforms the concrete into a water-resistant barrier. It becomes an integral part of the concrete matrix when applied to existing concrete or added to the mix at time of batching.
The crystalline waterproofing chemistry can be introduced into new concrete as an admixture, a dry-shake product, or a surface-applied coating. For older (i.e., cured) concrete, surface-applied coatings are used. The substrate must be wet for the chemicals to move through the concrete and for the chemical reaction to occur. With a surface coating application, the high concentration of chemicals at the surface naturally tends to spread out or diffuse into the water saturated substrate. Keeping the concrete moist maintains a conduit for the crystalline chemicals to travel.
Recently built structures and heritage buildings need water protection too! Whether we are waterproofing a new structure or repairing leaks, concrete waterproofing treatments allow us to turn existing concrete into a waterproof barrier reliably and cost-effectively
What are the benefits of Crystalline waterproofing over traditional membranes systems?
Unlike sheet membranes, which rely on an additional hurdle to shield the concrete from moisture, crystalline waterproofing system actually transforms the concrete into a water-resistant barrier. It becomes an integral part of the concrete matrix when applied to existing concrete or added to the mix at time of batching.
The crystalline waterproofing chemistry can be introduced into new concrete as an admixture, a dry-shake product, or a surface-applied coating. For older (i.e., cured) concrete, surface-applied coatings are used. The substrate must be wet for the chemicals to move through the concrete and for the chemical reaction to occur. With a surface coating application, the high concentration of chemicals at the surface naturally tends to spread out or diffuse into the water saturated substrate. Keeping the concrete moist maintains a conduit for the crystalline chemicals to travel.
Recently built structures and heritage buildings need water protection too! Whether we are waterproofing a new structure or repairing leaks, concrete waterproofing treatments allow us to turn existing concrete into a waterproof barrier reliably and cost-effectively
What are the benefits of Crystalline waterproofing over traditional membranes systems?
- Integrated – Crystalline waterproofing penetrates into the concrete. It will not crack, peel, tear or wear-away.
- Continually self-seals - Crystals within the concrete reactivate repeatedly over time to reseal cracks and prevent water penetration.
- Environmental – The products are non-toxic, non-flammable and odorless. This allows the concrete to be recycled.
- Traditional membrane systems are petroleum-based. They use adhesives with highly volatile organic compounds. The vapor from these compounds can cause respiratory problems and contribute to "sick building syndrome".
- Saves time – The products can be applied to green concrete or added to the ready-mix truck.
- Can be used from negative side of the concrete structures also unlike sheet membrane waterproofing systems which are recommended to use only from positive side.
- There is no need to wait for the membrane application, so backfilling can begin right away.
- Tropical climates - Membrane systems become brittle and deteriorate when exposed to prolonged heat. Crystalline systems reduce premature moisture loss in hot or tropical climates. It creates a more durable structure and reduces shrinkage and cracking. It is unaffected by climate and remains effective for the life of the structure.
Integral Crystalline Concrete Admixture
Crystalline Concrete Admixture Chryso CWA 10 consists of Portland cement, very fine treated silica sand and various active, proprietary chemicals. These active chemicals react with the moisture in fresh concrete with the by-products of cement hydration to cause a catalytic reaction, which generates a non-soluble crystalline formation throughout the pores and capillaries of the concrete. Thus the concrete becomes denser and permanently sealed against the penetration of water.
![Crystalline Concrete Admixture]()
It becomes an integral part of the concrete and it resists extreme hydrostatic pressures from either positive or negative surface of the concrete slab.
The function of Chryso CWA 10 is very much different than traditional integral waterproofing materials. It doesn't work on the principal of water repellency rather the active chemicals reacts with by-products of cement hydration and moisture/ water and forms insoluble crystals which permanently seals the voids/ capillaries in the concrete thereby making it denser.

It becomes an integral part of the concrete and it resists extreme hydrostatic pressures from either positive or negative surface of the concrete slab.
The function of Chryso CWA 10 is very much different than traditional integral waterproofing materials. It doesn't work on the principal of water repellency rather the active chemicals reacts with by-products of cement hydration and moisture/ water and forms insoluble crystals which permanently seals the voids/ capillaries in the concrete thereby making it denser.
How Crystalline Concrete Admixture Works?
When added to concrete, Crystalline admixture Chryso CWA 10 creates a reaction that causes long, narrow crystals to form, filling the pores, capillaries and hairline cracks of the concrete mass. As long as moisture remains present, crystals continue to grow throughout the concrete, reaching lengths of many inches over time. Once the concrete has cured, the crystalline chemicals sit dormant. It reactivate once it comes in contact of water (such as through a new crack) causing the chemical reaction to begin again. The ability to reactivate in the presence of water gives Chryso CWA 10-treated concrete the ability to "self-seal". When cracks form due to curing shrinkage, settling, seismic activity, etc., water entering through them causes new crystals to form and grow, blocking and filling the cracks.
![Integral Crystalline Concrete Admixture]()
Crystalline technology is based on principles that are very similar to the processes that occur during the hydration and hardening of concrete. When cement particles are mixed with water, a chemical reaction occurs where the Calcium Silicates present in cement combine with water molecules to form new compounds. The new compounds are Calcium Silicate Hydrate (CSH) and Calcium Hydroxide. The CSH forms as an amorphous microcrystalline structure, which extends outward from the cement particles and eventually fills the space between them. The CSH crystal formation is the mechanism by which the concrete hardens and gains strength. It is very rapid in the first hours after the concrete placement, but it actually continues for weeks, months and even years into the life of the concrete.
The reason that hydration can continue for a very long period, is because only a portion of the cement has reacted during the initial hydration and hardening process of the concrete. A significant portion of each cement particle remains un-reacted even long after the concrete has reached its design strength. These un-reacted particles allow the Chryso CWA 10 chemicals to perform their function. Chryso CWA 10 acts as a catalyst to a larger reaction within the concrete mass. Chryso CWA 10 forms hydration crystals that form into a crystalline structure of long hexagonal prisms that extend through and fill the capillary voids and micro-cracks of the concrete. The crystals themselves are not made up solely of the crystalline material, but grow from the partially reacted cement particles.
The Crystalline chemical is never used up during the crystallization process. As a catalyst, only a very small amount of crystalline chemical is required to grow a very large quantity of crystals. Within the tight confines of the concrete, crystals can easily grow to fill and block the microscopic capillary pores and micro-cracks without using more than a small fraction of the available Chryso CWA 10 chemical. The remaining chemical lies dormant within the concrete waiting for a crack to develop that will provide the necessary space and water source to allow the crystallization process to continue.

Crystalline technology is based on principles that are very similar to the processes that occur during the hydration and hardening of concrete. When cement particles are mixed with water, a chemical reaction occurs where the Calcium Silicates present in cement combine with water molecules to form new compounds. The new compounds are Calcium Silicate Hydrate (CSH) and Calcium Hydroxide. The CSH forms as an amorphous microcrystalline structure, which extends outward from the cement particles and eventually fills the space between them. The CSH crystal formation is the mechanism by which the concrete hardens and gains strength. It is very rapid in the first hours after the concrete placement, but it actually continues for weeks, months and even years into the life of the concrete.
The reason that hydration can continue for a very long period, is because only a portion of the cement has reacted during the initial hydration and hardening process of the concrete. A significant portion of each cement particle remains un-reacted even long after the concrete has reached its design strength. These un-reacted particles allow the Chryso CWA 10 chemicals to perform their function. Chryso CWA 10 acts as a catalyst to a larger reaction within the concrete mass. Chryso CWA 10 forms hydration crystals that form into a crystalline structure of long hexagonal prisms that extend through and fill the capillary voids and micro-cracks of the concrete. The crystals themselves are not made up solely of the crystalline material, but grow from the partially reacted cement particles.
The Crystalline chemical is never used up during the crystallization process. As a catalyst, only a very small amount of crystalline chemical is required to grow a very large quantity of crystals. Within the tight confines of the concrete, crystals can easily grow to fill and block the microscopic capillary pores and micro-cracks without using more than a small fraction of the available Chryso CWA 10 chemical. The remaining chemical lies dormant within the concrete waiting for a crack to develop that will provide the necessary space and water source to allow the crystallization process to continue.
Key Features of Chryso Crystalline Waterproofing System
- CHRYSO®CWA 10 forms crystals deep within the pores and the capillary tract of the concrete structure.
- After hydration, this chemical reaction remains dormant. However, with new traces of water, new crystals will form which will plug up the crack.
- CHRYSO®CWA 10 transforms the entire concrete structure into an impermeable water barrier with lasting integral waterproofing properties.
- Cracks are repaired optimally and simultaneously, unlike an externally applied waterproofing membrane.
- The crystals block the pores of the concrete, making it dense, waterproof and maintenance free.
- No significant change in fresh concrete properties (such as slump, retention and setting time) with addition of CWA 10 to concrete.
- No significant change in compressive strength of the concrete
Self Healing Properties of Chryso Cwa 10:
The most unique and effective feature is its ability to self-seal cracks, this can help to dramatically reduce the long-term maintenance and repair costs of a concrete structure.

- Micro cracks in concrete may appear due to settlement in buildings. Water then starts to travel through these cracks.
- CHRYSO®CWA 10 reacts with this seepage water to form crystals, which plug the crack and its surrounding capillaries.
- This process will trace the seepage water until it is completely plugged, thereby retaining the structure's original water tightness.
- These self healing properties are independently verified in accredited laboratories under stringent test conditions.

Measuring the Effectiveness of Chryso Crystalline Integral Waterproofing System
The effectiveness of any integral waterproofing system can be checked with following two criteria:
- Capillary Absorption (Depth of Water penetration from concrete surface)
- Permeability Test under Water Pressure (Coefficient of Water Permeability).
Capillary Absorption
In order to check the passage of the water through the only face in contact with water, the lateral faces of the cubes are made impermeable by gluing aluminum adhesive. The prepared test specimen is then made wet on a height of 1 cm all through the trial period.
A follow-up of the earth clamp is realized in order to determine the capillary absorption. Capillary absorption in 24 hours for different types of concrete has been measured.
A follow-up of the earth clamp is realized in order to determine the capillary absorption. Capillary absorption in 24 hours for different types of concrete has been measured.

Permeability in water under pressure
This trial aims at determining the coefficient of permeability for concrete in water. Free face of a cube 15x15x15 cm is exposed to water pressure. To guarantee that water penetrates through the cube from the superior exposed face, the lateral faces are resined then recovered from aluminum adhesive. Due to the pressure, the water traverses the test specimen through the height of the cube. The quantity of water passing through the test specimen is taken out at different instants for a period of 24 hours.

Conclusion
Although, concrete appears to be a simple product to be used in modern construction, still it requires a highly engineered approach. In an increasingly competitive design and construction environment, where high performance requirements, such as longer life cycles, more durable concrete, and value engineering are expected, careful consideration of basic requirements from concrete is very important and it requires careful mix design such as water and cement ratio; cementing materials, and more sophisticated chemical admixtures, etc.
Effective use of crystalline waterproofing technology will reduce the porosity and permeability of conventional concrete, and provide the high performance advantages and benefits that building owners and design professionals have come to rely upon in design and construction projects. Crystalline technology improves the durability and performance of concrete structures, lowering their maintenance cost and extending their lifespan by protecting them against the effect of aggressive chemicals.
Effective use of crystalline waterproofing technology will reduce the porosity and permeability of conventional concrete, and provide the high performance advantages and benefits that building owners and design professionals have come to rely upon in design and construction projects. Crystalline technology improves the durability and performance of concrete structures, lowering their maintenance cost and extending their lifespan by protecting them against the effect of aggressive chemicals.